In the automotive industry, the choice of connector materials significantly impacts performance and durability. Understanding the properties of different materials helps in selecting the most suitable connectors to ensure reliability and safety in automotive systems. Here is a comparison of the properties of common materials used in automotive connectors, to help you better understand their advantages and disadvantages.
Copper
Properties
- Electrical Conductivity: Copper has extremely high electrical conductivity and is commonly used for connectors due to its effective current transmission and minimal energy loss.
- Corrosion Resistance: Copper itself oxidizes easily in air but is usually plated with nickel or tin to enhance its corrosion resistance.
- Workability: Copper is easy to process and form, making it suitable for complex connector designs.
Applications
- Used in connectors requiring high current transmission, such as power connectors and engine connectors.
- Ideal for automotive systems with strict electrical current demands.
Aluminum
Properties
- Lightweight: Aluminum is lighter than copper, which helps reduce the overall weight of connectors and improves fuel efficiency.
- Electrical Conductivity: Aluminum’s conductivity is lower than copper but sufficient for some applications.
- Corrosion Resistance: Aluminum has good corrosion resistance, especially when anodized.
Applications
- Used in components where weight reduction is crucial, such as body connectors.
- Suitable for low-current applications in connectors.
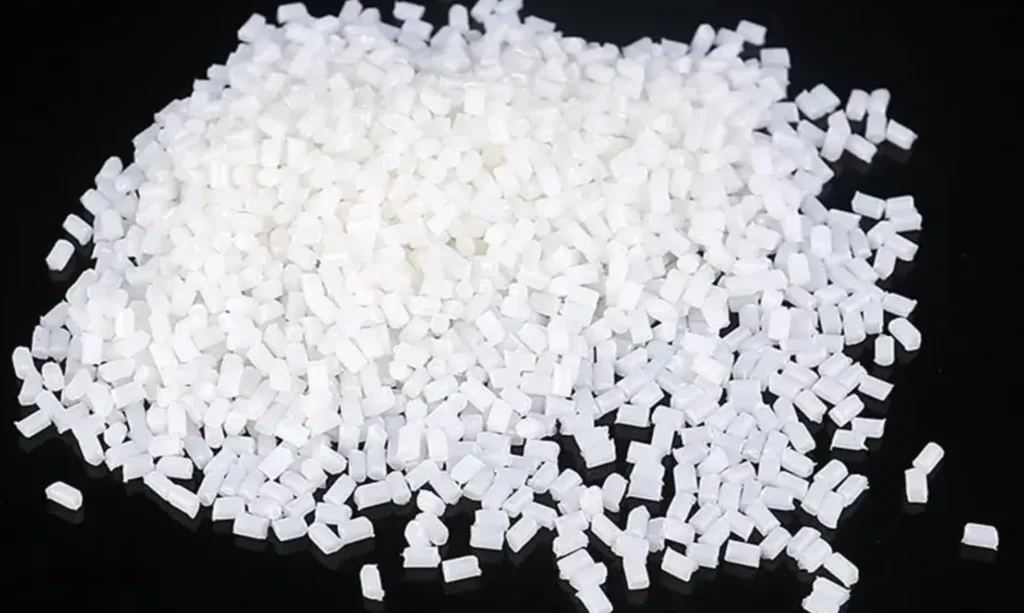
Stainless Steel
Properties
- Corrosion Resistance: Stainless steel offers excellent corrosion resistance, making it ideal for harsh environments such as high humidity or salt spray conditions.
- Strength: Stainless steel has high mechanical strength and wear resistance.
- Electrical Conductivity: Stainless steel has lower electrical conductivity and is typically used in structural components rather than electrical connections.
Applications
- Used in structural parts of automotive connectors, such as housings and fasteners.
- Suitable for connectors in extreme environments.
Plastic
Properties
- Insulation: Plastic provides excellent insulation properties, making it suitable for applications requiring electrical isolation.
- Lightweight: Plastic is lightweight, contributing to a reduction in overall connector weight.
- Temperature Resistance: Various plastics have different temperature resistance, so the right type must be chosen based on specific requirements.
Applications
- Used in the housings and insulation parts of automotive connectors.
- Ideal for low-current and low-temperature applications.
Copper-Nickel Alloy
Properties
- Electrical Conductivity: Copper-nickel alloys offer better conductivity than pure copper and have higher corrosion resistance.
- Wear Resistance: The alloy has good wear resistance, suitable for connectors with frequent mating and unmating.
- Cost: Copper-nickel alloy is more expensive than pure copper but provides superior performance and durability.
Applications
- Used in high-end automotive connectors, particularly where high performance and durability are required.
- Suitable for connectors in frequent mating and harsh environments.
Summary
Selecting the right connector material is crucial for ensuring the performance and reliability of automotive systems. Each material has unique advantages and applications. Understanding their properties helps in making informed choices to optimize connector performance and longevity.