As the complexity of aircraft electrical systems has increased, single-interface connections have become inadequate, particularly in military applications where electrical components often require over ten connection points. These connections must remain secure under harsh conditions while allowing for rapid disconnection for maintenance, which is especially critical during combat scenarios.
In response, American aircraft manufacturers adopted a solution originating from the dynamic projection industry in the early 1920s. In 1925, founder Robert Cannon introduced the M series, featuring sockets and plugs with a mechanical locking ring designed to prevent accidental disconnections in studio lighting applications. By the late 1920s, the P series connectors, equipped with a pin-locking mechanism, were developed for new sound film cameras, while Fox Film Corporation introduced a threaded coupling ring design variant.
Building on these innovations, threaded ring circular connectors were deemed most suitable for aviation applications and were first utilized in the DC-1 aircraft. The cylindrical connectors consist of two mating half-shells, each containing multiple sets of socket configurations. Internally, they are supported by insulating spacers originally made of hard rubber, ensuring the correct positioning of the contact elements. One end of the plug connects to the wire harness, while the socket is typically fixed to a surface such as a panel.
The plug comprises three components: the body, coupling nut, and rear mid-section. The body fits into the socket housing and is secured by the coupling nut. To prevent damage during separation or closure of the half-shells, the alignment of the pins with the sockets must strictly adhere to established standards. Wires are connected to the contact pins through crimping or soldering and are secured using interference locks, contact locks, or insertion locks.
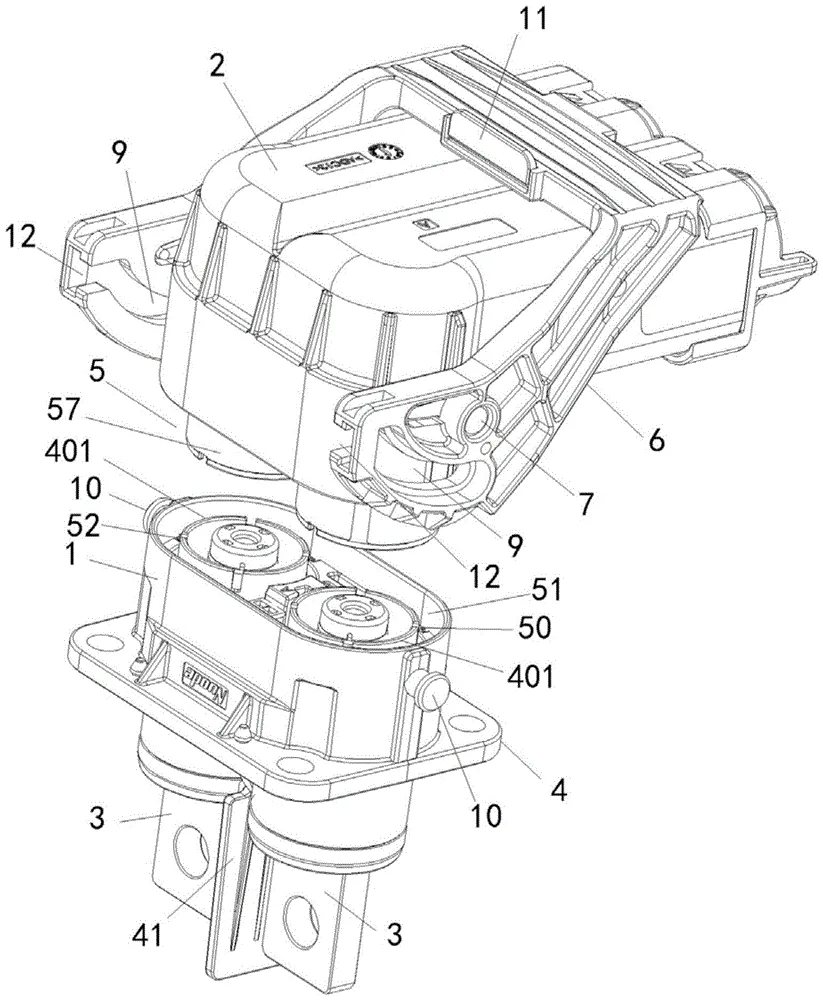
The locking mechanisms dictate how the pins connect to the housing, which is generally constructed from aluminum or steel for structural integrity. Furthermore, these housings undergo polarization treatment to prevent mismatching and facilitate assembly.
The widespread adoption of such connectors prompted the U.S. Department of Defense to establish military standards aimed at providing a range of standardized components with precisely defined shell sizes and pin layouts. These components are specifically designed and tested to ensure reliability, performance, and environmental adaptability for intended applications. The initial military standard, AN-9534, was issued on November 1, 1934, and was later replaced by AN-WC-591 two years later, undergoing several revisions during World War II.
During this period, as aerial combat capabilities were enhanced, the U.S. military significantly elevated its focus on aviation forces, ultimately leading to the establishment of the United States Air Force as an independent branch of the military. This transformation ushered in a series of new electrical connector technologies, culminating in 1949 with the adoption of the MLC-5015 military standard, which unified electrical connector specifications recognized by the Army, Navy, and Air Force.
The MIL-C-5015 standard specified a broad range of contact sizes and applications up to 3,000 volts of alternating current. Breakthroughs in synthetic polymer technology during the 1920s and 1930s brought revolutionary changes to the electrical industry. Compared to traditional impregnated fabrics and fully rubber insulation, plastics exhibited superior performance, particularly in abrasion resistance and resistance to electrical and thermal degradation.
Unlike previous insulating materials, plastics can be tailored to meet a wider range of application needs by adjusting their physical properties. Among these, PVC emerged as the most widely used plastic for wire and cable insulation in its early applications. During World War II, due to severe shortages of natural rubber, PVC was promoted as a substitute for rubber insulation. The thermoplastic nature of PVC facilitates easy processing, as it softens when heated and hardens upon cooling.
Moreover, by incorporating stabilizers, plasticizers, flame retardants, and lubricants, PVC can exhibit diverse properties. PVC insulation designs can withstand temperatures ranging from -40 degrees Celsius to 125 degrees Celsius, as well as resist abrasion, moisture, and ultraviolet light. Its safe insulating voltage can reach up to 1,000 volts. However, PVC may degrade or catalyze in contact with hydrocarbons and chlorinated solvents, increasing the risk of insulation failure. In low-temperature environments, PVC may lose flexibility, becoming hard and brittle, while in the presence of fire, it can release dense smoke, hydrochloric acid gas, and highly toxic dioxins, posing significant threats to health and the environment.